అధిక-ఖచ్చితమైన కొలిచే పరికరంగా, పనిలో CMM, కొలత ఖచ్చితత్వ లోపం వల్ల కలిగే కొలిచే యంత్రంతో పాటు, కొలత లోపాల వల్ల కొలిచే యంత్రం యొక్క ఖచ్చితత్వాన్ని ప్రభావితం చేసే అనేక అంశాలు ఉన్నాయి.ఆపరేటర్ ఈ లోపాల కారణాలను అర్థం చేసుకోవాలి, అన్ని రకాల లోపాలను వీలైనంత వరకు తొలగించాలి మరియు భాగాల కొలత యొక్క ఖచ్చితత్వాన్ని మెరుగుపరచాలి.
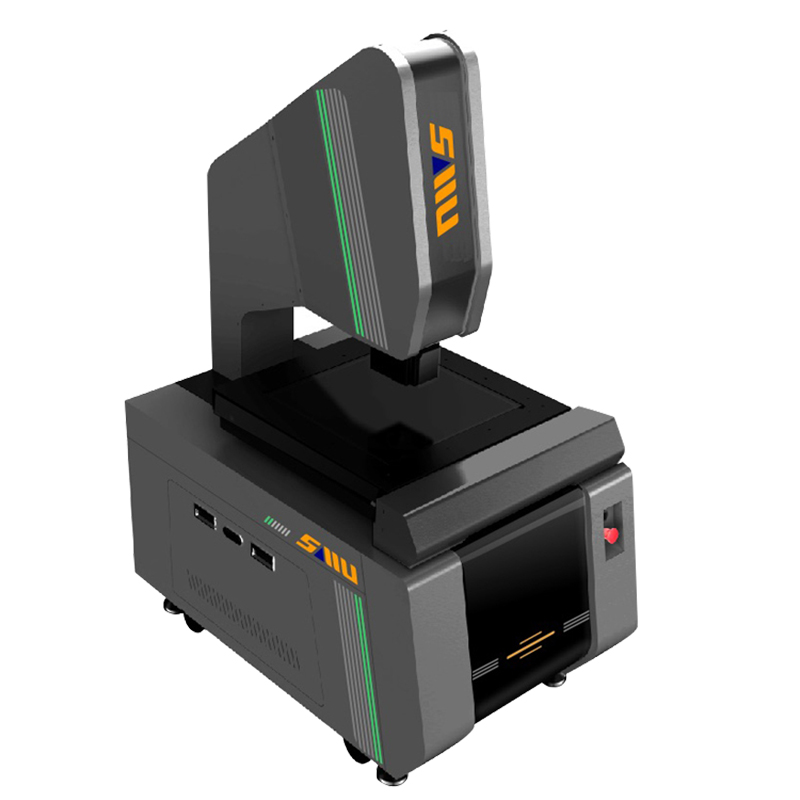
CMM ఎర్రర్ సోర్స్లు అనేకం మరియు సంక్లిష్టమైనవి, సాధారణంగా CMM యొక్క ఖచ్చితత్వంపై సాపేక్షంగా పెద్ద ప్రభావాన్ని చూపే ఎర్రర్ సోర్స్లు మరియు ప్రధానంగా కింది ప్రాంతాలలో వేరు చేయడం సులభం.
1. ఉష్ణోగ్రత లోపం
ఉష్ణోగ్రత లోపం, థర్మల్ ఎర్రర్ లేదా థర్మల్ డిఫార్మేషన్ ఎర్రర్ అని కూడా పిలుస్తారు, ఇది ఉష్ణోగ్రత యొక్క లోపం కాదు, కానీ ఉష్ణోగ్రత కారకం వల్ల ఏర్పడే రేఖాగణిత పారామితుల కొలత లోపం.ఉష్ణోగ్రత లోపం ఏర్పడటానికి ప్రధాన కారకం కొలిచిన వస్తువు మరియు కొలిచే పరికరం యొక్క ఉష్ణోగ్రత 20 డిగ్రీల నుండి వైదొలగడం లేదా కొలిచిన వస్తువు యొక్క పరిమాణం మరియు పరికరం యొక్క పనితీరు ఉష్ణోగ్రతతో మారుతుంది.
పరిష్కారం.
1) ఫీల్డ్ క్రమాంకనం సమయంలో పర్యావరణ పరిస్థితుల కోసం ఉష్ణోగ్రత యొక్క ప్రభావాన్ని సరిచేయడానికి కొలిచే యంత్రం యొక్క సాఫ్ట్వేర్లో లీనియారిటీ కరెక్షన్ మరియు ఉష్ణోగ్రత దిద్దుబాటును ఉపయోగించవచ్చు.
2) ఎలక్ట్రికల్ పరికరాలు, కంప్యూటర్లు మరియు ఇతర ఉష్ణ వనరులను కొలిచే యంత్రం నుండి కొంత దూరంలో ఉంచాలి.
3) ఎయిర్ కండిషనింగ్ బలమైన ఉష్ణోగ్రత నియంత్రణ సామర్థ్యంతో ఇన్వర్టర్ ఎయిర్ కండీషనర్ను ఎంచుకోవడానికి ప్రయత్నించాలి మరియు ఎయిర్ కండీషనర్ యొక్క ఇన్స్టాలేషన్ స్థానం సహేతుకంగా ప్రణాళిక చేయబడాలి.ఎయిర్ కండీషనర్ గాలి దిశను కొలిచే యంత్రంపై నేరుగా వీచడం నిషేధించబడింది మరియు ఎగువ మరియు దిగువ కొలిచే గది మధ్య ఉష్ణోగ్రత వ్యత్యాసం కారణంగా ఇండోర్ గాలి ఉష్ణోగ్రతను సమతుల్యంగా ఉంచడానికి గాలి పెద్ద ప్రసరణను ఏర్పరచడానికి గాలి దిశను పైకి సర్దుబాటు చేయాలి. స్థలం.
4) ప్రతిరోజూ ఉదయం పని వద్ద ఎయిర్ కండీషనర్ను తెరిచి, రోజు చివరిలో దాన్ని మూసివేయండి.
5) మెషిన్ గదిలో వేడి సంరక్షణ చర్యలు ఉండాలి, ఉష్ణోగ్రత వెదజల్లడానికి మరియు సూర్యరశ్మిని నివారించడానికి గది తలుపులు మరియు కిటికీలు మూసివేయబడాలి.
6) కొలత గది నిర్వహణను బలోపేతం చేయండి, అదనపు వ్యక్తులు ఉండకూడదు.
2. ప్రోబ్ క్రమాంకనం లోపం
ప్రోబ్ కాలిబ్రేషన్, కాలిబ్రేషన్ బాల్ మరియు స్టైలస్ శుభ్రంగా లేవు మరియు దృఢంగా లేవు మరియు తప్పు స్టైలస్ పొడవు మరియు స్టాండర్డ్ బాల్ వ్యాసం ఇన్పుట్ చేయడం వలన కొలత సాఫ్ట్వేర్ను ప్రోబ్ కాంపెన్సేషన్ ఫైల్ పరిహారం లోపం లేదా ఎర్రర్ అని పిలుస్తుంది, ఇది కొలత ఖచ్చితత్వాన్ని ప్రభావితం చేస్తుంది.సరికాని స్టైలస్ పొడవులు మరియు ప్రామాణిక బాల్ డయామీటర్లు కొలత సమయంలో ప్రోబ్ పరిహారం ఫైల్ను సాఫ్ట్వేర్ కాల్ చేసినప్పుడు పరిహారం లోపాలు లేదా పొరపాట్లకు కారణమవుతాయి, కొలత ఖచ్చితత్వాన్ని ప్రభావితం చేస్తాయి మరియు అసాధారణమైన ఘర్షణలు మరియు పరికరాలకు నష్టం కలిగించవచ్చు.
పరిష్కారం:
1) స్టాండర్డ్ బాల్ మరియు స్టైలస్ శుభ్రంగా ఉంచండి.
2) తల, ప్రోబ్, స్టైలస్ మరియు స్టాండర్డ్ బాల్ సురక్షితంగా బిగించబడిందని నిర్ధారించుకోండి.
3) సరైన స్టైలస్ పొడవు మరియు ప్రామాణిక బంతి వ్యాసాన్ని నమోదు చేయండి.
4) ఆకార లోపం మరియు క్రమాంకనం చేసిన బంతి వ్యాసం మరియు పునరావృతత ఆధారంగా క్రమాంకనం యొక్క ఖచ్చితత్వాన్ని నిర్ణయించండి (కాలిబ్రేటెడ్ బాల్ వ్యాసం పొడిగింపు పట్టీ యొక్క పొడవుపై ఆధారపడి ఉంటుంది).
5) వేర్వేరు ప్రోబ్ స్థానాలను ఉపయోగిస్తున్నప్పుడు, అన్ని ప్రోబ్ స్థానాలను క్రమాంకనం చేసిన తర్వాత ప్రామాణిక బంతి యొక్క సెంటర్ పాయింట్ యొక్క కోఆర్డినేట్లను కొలవడం ద్వారా అమరిక ఖచ్చితత్వాన్ని తనిఖీ చేయండి.
6) ప్రోబ్లో, స్టైలస్ మూవ్ చేయబడింది మరియు రీకాలిబ్రేట్ చేయాల్సిన ప్రోబ్ విషయంలో కొలత ఖచ్చితత్వ అవసరాలు సాపేక్షంగా ఎక్కువగా ఉంటాయి.
3. కొలత సిబ్బంది లోపం
ఏదైనా పనిలో, ప్రజలు ఎల్లప్పుడూ లోపానికి దారితీసే ముఖ్యమైన కారకాల్లో ఒకరు, CMM యొక్క ఆపరేషన్లో, సిబ్బంది లోపం తరచుగా సంభవిస్తుంది, ఈ లోపం సంభవించడం మరియు సిబ్బంది మరియు సాంస్కృతిక నాణ్యత యొక్క వృత్తిపరమైన స్థాయి ప్రత్యక్ష సంబంధం కలిగి ఉంటుంది, CMM అనేది ఖచ్చితమైన పరికరాలలో ఒకదానిలో వివిధ రకాలైన హైటెక్ టెక్నాలజీ, కాబట్టి ఆపరేటర్కు కఠినమైన అవసరాలు ఉన్నాయి, ఒకసారి ఆపరేటర్ యంత్రాన్ని సరిగ్గా ఉపయోగించకపోతే, ఆపరేటర్ యంత్రాన్ని సరిగ్గా ఉపయోగించకపోతే, అది లోపానికి దారి తీస్తుంది.
పరిష్కారం:
అందువల్ల, CMM యొక్క ఆపరేటర్కు వృత్తిపరమైన సాంకేతికత అవసరం మాత్రమే కాకుండా, పని పట్ల ఉత్సాహం మరియు బాధ్యత యొక్క అధిక స్థాయిని కలిగి ఉంటుంది, కొలిచే యంత్రం యొక్క ఆపరేషన్ సూత్రం మరియు నిర్వహణ పరిజ్ఞానంతో సుపరిచితం, యంత్రం యొక్క ఆపరేషన్లో సమర్థవంతంగా ఆడవచ్చు. ఫంక్షనల్ కొలిచే యంత్రం, మరియు దాని పని యొక్క ప్రభావాన్ని మెరుగుపరచడం, తద్వారా సంస్థ కోసం అత్యధిక ఆర్థిక ప్రయోజనాలను పొందడం.
4. కొలత పద్ధతి లోపం
కోఆర్డినేట్ కొలిచే యంత్రం డైమెన్షనల్ లోపాలు మరియు భాగాలు మరియు భాగాల యొక్క డైమెన్షనల్ టాలరెన్స్లను కొలవడానికి ఉపయోగించబడుతుంది, ముఖ్యంగా డైమెన్షనల్ టాలరెన్స్ల కొలత కోసం, ఇది అధిక ఖచ్చితత్వం, అధిక సామర్థ్యం మరియు పెద్ద కొలత పరిధి యొక్క ప్రయోజనాలను చూపుతుంది మరియు డైమెన్షనల్ కోసం అనేక రకాల కొలత పద్ధతులు ఉన్నాయి. టాలరెన్స్లు, డైమెన్షనల్ టాలరెన్స్లను కొలిచేందుకు ఉపయోగించే గుర్తింపు సూత్రం సరిగ్గా లేకుంటే, ఎంచుకున్న పద్ధతి ఖచ్చితమైనది కాదు, కఠినమైనది కాదు, ఖచ్చితమైనది కాదు, అది కొలత పద్ధతిలో లోపాలను కలిగిస్తుంది.
పరిష్కారం:
అందువల్ల, CMM యొక్క పనిలో నిమగ్నమై ఉన్నవారు తప్పనిసరిగా కొలత పద్ధతులతో సుపరిచితులై ఉండాలి, ప్రత్యేకించి గుర్తింపు సూత్రాలు మరియు ఫారమ్ టాలరెన్స్ యొక్క కొలత పద్ధతులు కొలత పద్ధతుల యొక్క లోపాన్ని తగ్గించడానికి చాలా సుపరిచితం.
5. కొలిచిన వర్క్పీస్ యొక్క లోపం
ఎందుకంటే మెషిన్ మెజర్మెంట్ను కొలిచే సూత్రం మొదట పాయింట్లను తీసుకోవడం, ఆపై సాఫ్ట్వేర్ పాయింట్లను సరిపోయేలా తీసుకోవడం మరియు లోపాన్ని లెక్కించడం.కాబట్టి భాగం లోపం యొక్క ఆకారం యొక్క కొలత యంత్రం కొలతకు కొన్ని అవసరాలు ఉన్నాయి.కొలిచిన భాగాలలో స్పష్టమైన బర్ర్స్ లేదా ట్రాకోమా ఉన్నప్పుడు, కొలత యొక్క పునరావృతత గణనీయంగా అధ్వాన్నంగా మారుతుంది, తద్వారా ఆపరేటర్ ఖచ్చితమైన కొలత ఫలితాలను ఇవ్వలేరు.
పరిష్కారం:
ఈ సందర్భంలో, ఒక వైపు, కొలిచిన భాగం యొక్క ఆకార దోషాన్ని నియంత్రించాల్సిన అవసరం ఉంది మరియు మరోవైపు, కొలిచే రాడ్ యొక్క రత్నపు బంతి యొక్క వ్యాసాన్ని తగిన విధంగా పెంచవచ్చు, కానీ కొలత లోపం స్పష్టంగా పెద్దదిగా ఉంటుంది. .
పోస్ట్ సమయం: అక్టోబర్-21-2022